Study of breakage point of sealed tube ends
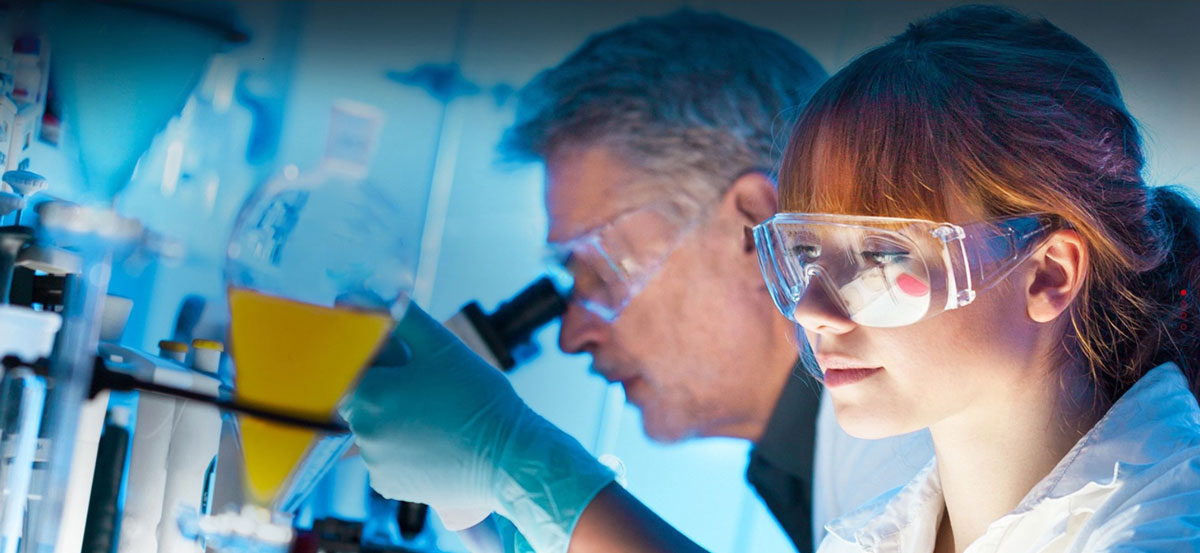
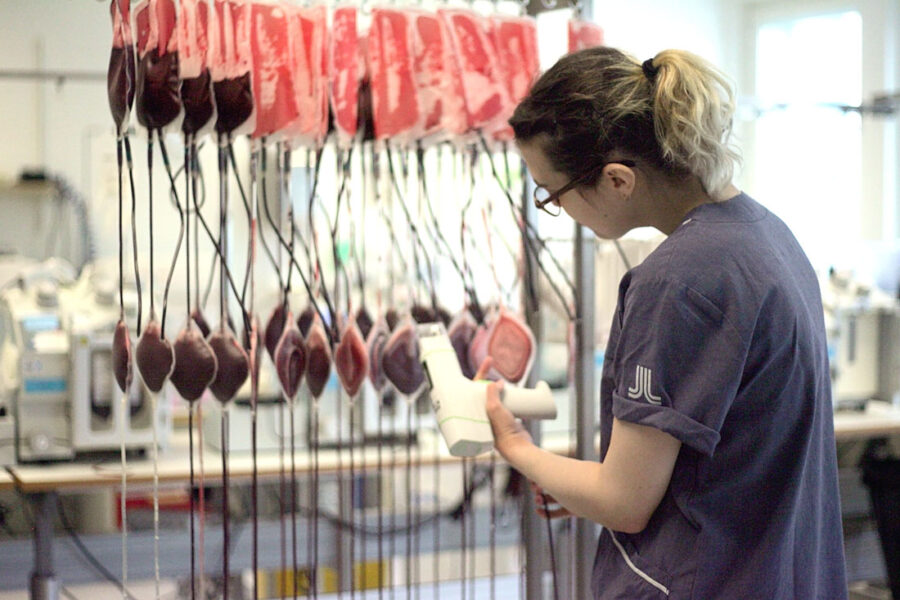
Breakage point of sealed tube ends exposed to severe mechanical stress is impacted by choice of sealing equipment
Linda Larsson, Julia Derving & Hanna-Stina Ahlzén at the Department of Clinical Immunology and Transfusion Medicine, Karolinska University Hospital, Stockholm, Sweden. Linda also at Department of Clinical Science, Intervention and Technology (CLINTEC), Karolinska Institutet, Stockholm, Sweden.
Background
Tube sealing is a pivotal part of blood processing. It is important that seals withstand mechanical stress, since they are exposed to large forces and rapid temperature changes within large intervals. We have previously studied the impact of centrifugal force on seals by a single sealer in combination with tubes containing different amounts of plasticiser DEHP (di-2-ethylhexyl phtalate). Now, we want to expand our knowledge to include several sealers from different manufacturers and extended strength testing.
Aim
The aim of the study was to investigate how seals made with multiple types of sealing equipment resist mechanical stress, and a possible link to DEHP content of tube.
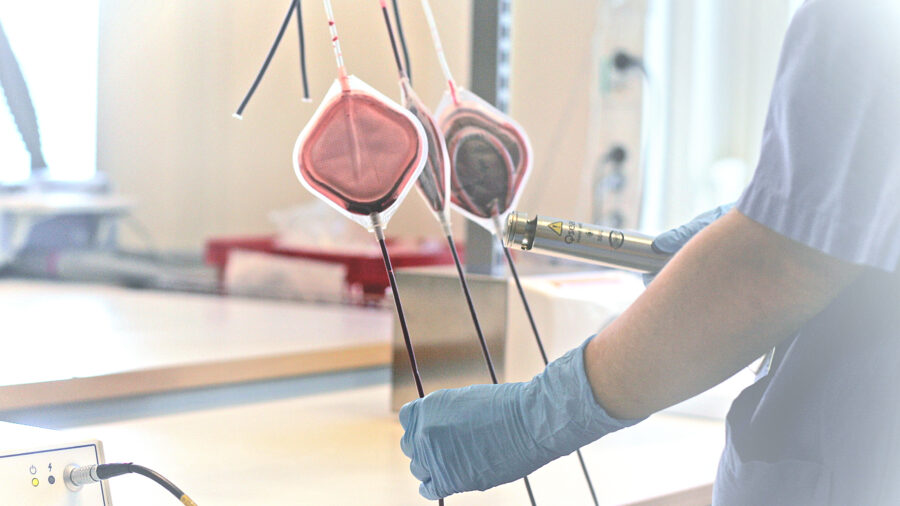
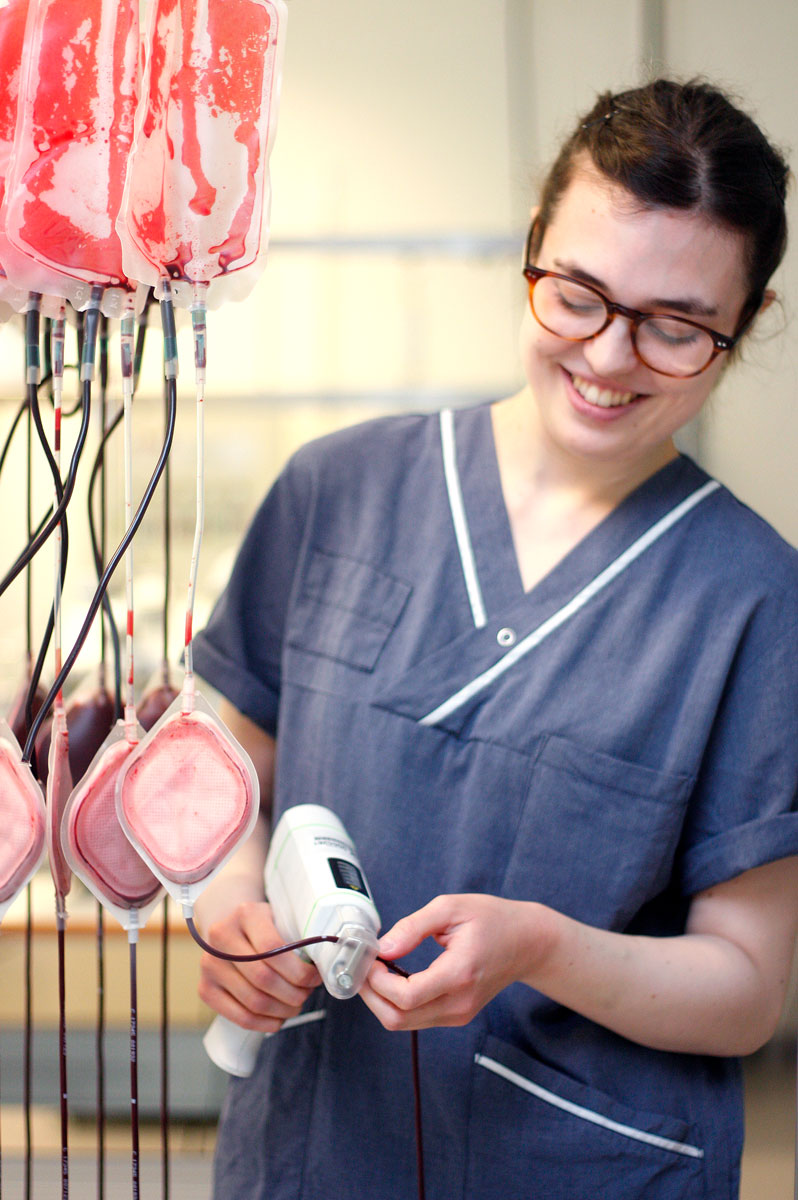
Method
Starting material
PVC-tubes from blood collection bags containing 35% (Teruflex transfer bag, TerumoBCT) or 32% (NPT6820LE, MacoPharma) DEHP were filled with whole blood containing CPD, from a randomly selected donor.
Sealing and further processing
Seals were created at every 5–10 cm of tube using the following panel of sealers: A) Qseal-free (Conroy Medical), B) CompoSeal Mobilea (Fresenius Kabi), C) Sebra model 2600 (Sebra), and D) Möller Medical/Docon seal handle (Möller Medical). All sealing was performed with tubes and content in room temperature. The seals were inspected to avoid that defect seals were included in the study. They were then separated, cut in segments (2.5 cm from each sealed end), washed with water and thereafter air-dried.
Testing
Two kinds of strength tests were performed:
Test 1: Segments (10 per tube type and sealer) were connected to an air pressure regulator (MINI REG 08A, Atlas Copco). Sealed tube ends were submerged in water to enable detection of small leakages. Air was pressed into each segment, from 0.5 to 10 bar, with measure points at each integer, where pressure was held for 2 seconds each.
Test 2: Segments (20 per tube type and sealer) were filled with water and stripped with a manual tube stripper (Lmb Technologie) until breakage, thereafter inspected with magnifying glass.
Results
Test 1: All segments resisted 10 bar pressure without breaking for sealer A, B and D. One segment from sealer C, containing 32%-DEHP, broke in the seal at 7 bar pressure.
Test 2: All segments made by sealer C broke in the seal. The segments from B broke similarly, except 10% of 32%-DEHP tubes where the tube broke (seal intact). For segments from D, 30% of 35%-DEHP and 15% of 32%-DEHP tubes broke in the seal. None of the segments from A broke in the seal.
Results from Test 2.
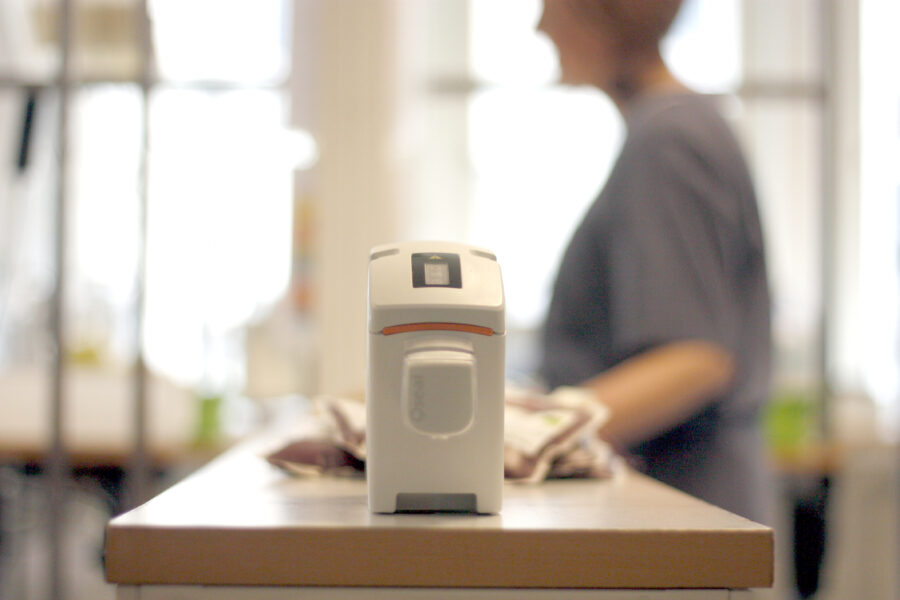
Summary
The purpose of a sealer is to create and keep a closed system. Seals are generally very resistant to large forces; however, they can be forced to break by severe mechanical stress. The point of breakage, i.e. seal versus tube, depends on the type of sealer used, meaning there is a quality difference in sealing patterns depending on equipment.
Whether the DEHP content of the tube affects the point of breakage is inconclusive, but it may possibly be related to seal mechanics or temperature. This needs to be further investigated.
Conclusion
A seal should not, and does not have to, represent the weakest point in a closed system. Breakage in the seal is avoidable. Therefore, sealing equipment should be chosen with great care.